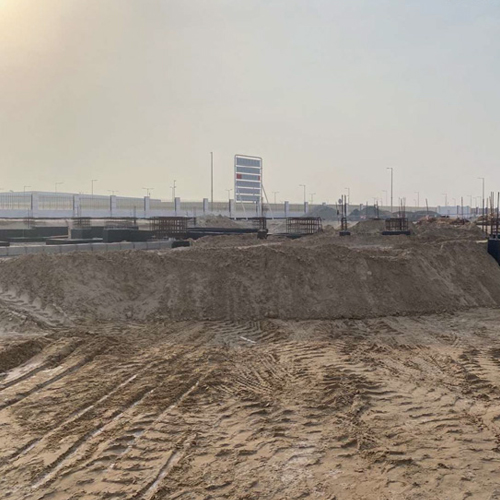
The Art of Warehouse Construction: Designing Spaces for Maximum Efficiency
Abrar Infra, a Warehouse Construction Company in Dubai, UAE plays a crucial role in shaping the efficient and innovative design of warehouses in the region. With the growing demand for logistics and distribution services, the expertise of a Warehouse Contracting Company in Dubai, UAE becomes paramount to create state-of-the-art facilities that cater to diverse industry needs. We as a Warehouse Contracting Company in Dubai, UAE bring a wealth of experience in designing and constructing warehouses that optimize space, streamline operations, and incorporate the latest technological advancements. From layout optimization to flow management and strategic storage system placement, We ensure that warehouses are built for maximum efficiency and cost-effectiveness.
- The Foundation: Analysing Needs and Objectives
Before embarking on the warehouse construction journey, it is essential to thoroughly understand the company’s needs, objectives, and unique requirements. The warehouse’s purpose, industry, and the nature of the goods to be stored are key factors that influence the design process. For example, an e-commerce fulfillment center would have distinct needs compared to a manufacturing warehouse.
Conducting a thorough analysis of inventory turnover rates, product dimensions, storage capacities, and anticipated growth projections provides a solid foundation for warehouse design. An expert team of architects, engineers, and warehouse specialists can work collaboratively to tailor the space to specific operational demands.
Optimizing Layout for Efficiency
An efficient layout is the cornerstone of any well-designed warehouse. The goal is to minimize the time and effort spent on material handling, thus optimizing productivity and reducing operational costs. Key considerations when optimizing layout include:
1. Zoning:
Categorizing different areas based on their functions, such as receiving, storage, picking, packing, and shipping. This zoning facilitates smoother workflows and prevents cross-contamination of products.
2. Aisle Width:
Striking the right balance between aisle width and storage capacity is crucial. Narrower aisles maximize storage space but can slow down movement, while wider aisles increase maneuverability but reduce storage efficiency.
3. Flow Patterns:
Implementing logical flow patterns ensures that material handling processes are streamlined. For example, placing receiving docks close to the storage area can expedite inventory replenishment.
4. Flexibility:
Anticipating future changes and incorporating flexibility into the design allows the warehouse to adapt to evolving business needs.
- Managing Flow for Seamless Operations
Efficient flow management is the art of orchestrating the movement of goods through the warehouse seamlessly. A well-organized workflow reduces bottlenecks, minimizes congestion, and optimizes order fulfillment.
Key considerations for flow management include:
1. Pick-and-Pack Process:
Analyzing order picking patterns and grouping frequently ordered items closer together can significantly reduce travel time and increase picking efficiency.
2. Cross-Docking:
For high-velocity goods with minimal storage requirements, cross-docking allows for direct transfer from inbound to outbound shipments, bypassing long-term storage.
3. Automated Systems:
Implementing conveyors, sortation systems, and robotics can automate material movement, further streamlining the flow within the warehouse.
4. Integration with Technology:
Leveraging Warehouse Management Systems (WMS) and real-time data analytics enhances visibility and improves decision-making for operational efficiency.
- The Art of Strategic Storage System Placement
Storage systems play a pivotal role in warehouse design, and strategic placement can significantly impact accessibility, storage capacity, and ease of material handling. Various storage options are available, each catering to specific requirements:
1. Pallet Racking:
Ideal for storing large quantities of palletized goods, pallet racking offers maximum storage density with direct access to each pallet.
2. Cantilever Racks:
Suitable for storing long and bulky items, cantilever racks provide easy access and efficient space utilization.
3. Mezzanine Flooring:
Utilizing vertical space efficiently, mezzanines create additional storage capacity without expanding the warehouse’s physical footprint.
4. Automated Storage and Retrieval Systems (AS/RS):
AS/RS systems offer high-density storage with automated retrieval, reducing labor costs and improving inventory accuracy.
By carefully selecting and placing storage systems based on the characteristics of the goods, warehouse managers can optimize space usage and ensure swift retrieval, thus reducing unnecessary delays and costs.
- Harnessing Technology for Greater Efficiency
Embracing technology is a fundamental aspect of modern warehouse design. The integration of smart systems and automation solutions can elevate operational efficiency to unprecedented levels:
1. Warehouse Management Systems (WMS):
WMS software optimizes inventory management, order processing, and workforce allocation, leading to reduced errors and increased accuracy.
2. Internet of Things (IoT):
IoT devices can monitor inventory levels, temperature, and other critical parameters in real-time, helping businesses make informed decisions and prevent stockouts or spoilage.
3. Robotics and AGVs:
Incorporating robots and Autonomous Guided Vehicles (AGVs) into warehouse operations minimizes manual labor, enhances picking accuracy, and accelerates order fulfillment.
4. Machine Learning and Predictive Analytics:
Utilizing advanced analytics enables businesses to forecast demand, optimize inventory levels, and make data-driven decisions for cost reduction.
Conclusion
In the art of warehouse construction, thoughtful design lies at the heart of efficiency, productivity, and cost-effectiveness. By optimizing layout, managing flow, strategically placing storage systems, and harnessing technology, we can create warehouses that operate at your peak potential.
A well-designed warehouse space not only facilitates smoother operations and streamlined material handling but also contributes to a safer and more conducive working environment. As the logistics landscape continues to evolve, embracing the art of warehouse construction will undoubtedly be a strategic advantage, enabling our clients to meet customer demands, scale operations, and stay ahead of the competition in the ever-changing global marketplace.
Tags -: Construction companies for a warehouse in Dubai, UAE & Construction company for a warehouse in Dubai, UAE